Destroyed propulsion system Turbocharger damage Load simulation of a connecting rod bushing
Damage to machinery and plant can not only have considerable economic consequences, but often also entail the risk of endangering people, equipment and the environment. Technical failures and accidents must therefore be avoided at all costs. This can only be achieved if the causes of the damage that has occurred are precisely clarified and effective measures are taken to prevent such damage in the future. The core of the strategy we pursue is simulation-based damage analysis.
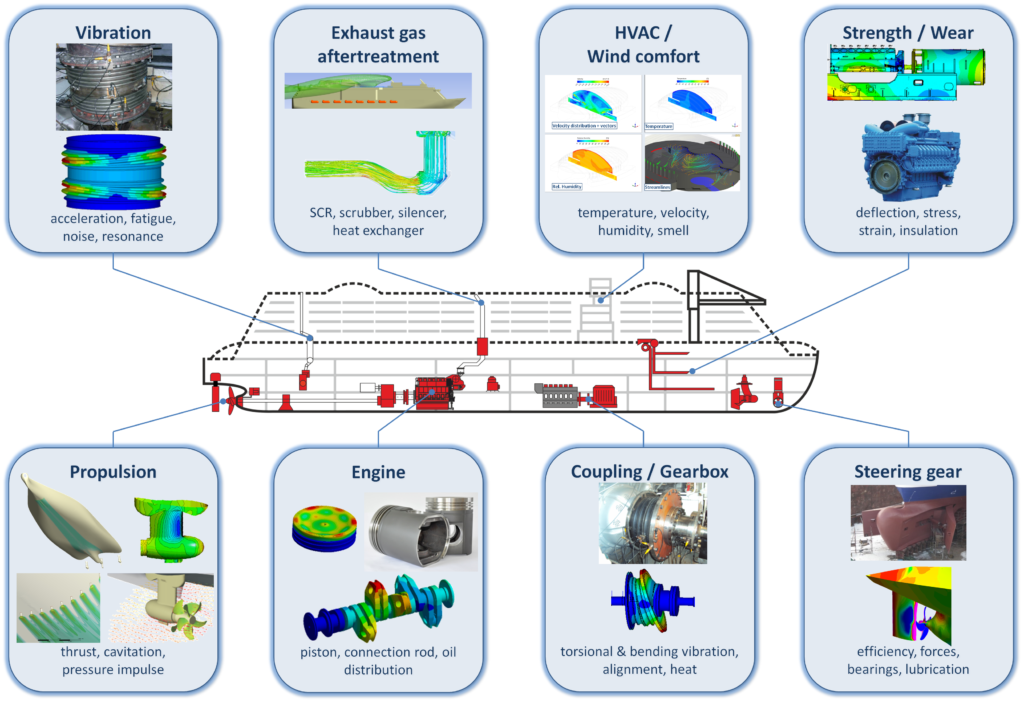
More than 25 years of experience with damage to components and machines from various industrial sectors, such as shipbuilding, aircraft construction and plant construction as well as propulsion, environmental and energy technology, combined with the application of modern experimental and computational methods, enable us to reliably and accurately identify the causes of damage and the process by which it occurs. To this end, we examine the damage pattern, simulate the process, describe the damage scenario and summarize the findings in a clear damage report. This then provides the basis for the short-term recommissioning of the affected plants and facilities, often with novel solutions.
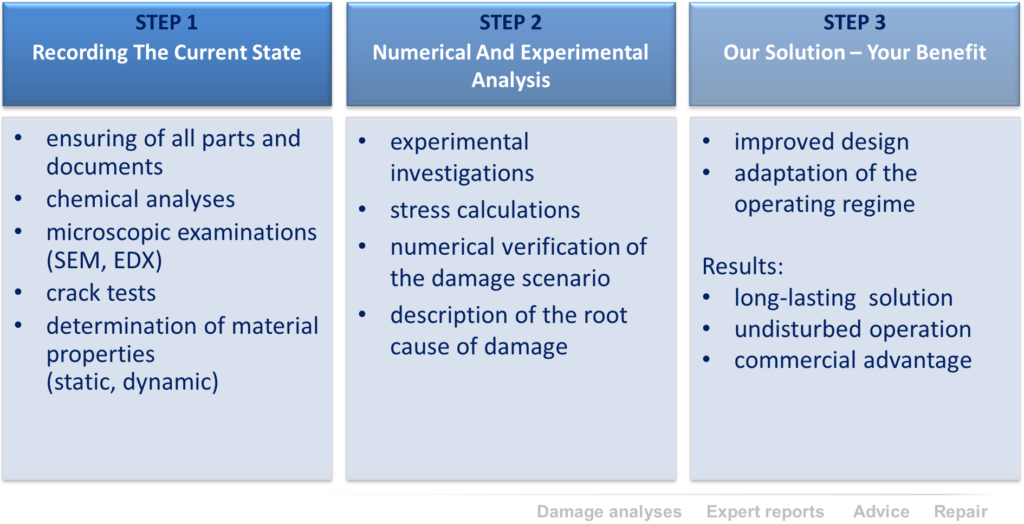
Root Cause Analysis
High-temperature corrosion on a piston Microscopic analysis Gearing stress Crack testing
If a failure of a component or a plant has occurred, a rapid recording of the situation on site and comprehensive documentation of the course and circumstances of the event is required. After a corresponding enquiry, our experts immediately go to the site of the incident to document the condition there and thus create the basis for further investigations and assessments. In emergencies, we are available around the clock.
The damaged parts are then returned to the owner or to us for a detailed inspection. In addition to fracture patterns and deformations, versatile material analyses also form the basis for further considerations. If this information and analytical calculations are not sufficient to give a plausible explanation of the damage, we develop numerical models based on the collected geometry, material and operating data. These are used to simulate certain load situations or processes in order to reproduce the component behavior realistically and thus clarify the cause of the damage.
Expert Report
Series investigation turbocharger Bearing bush Cylinder heads
The introduction of a product has been successfully completed, the component is functioning properly for a long time within the operating and maintenance parameters defined by the manufacturer… Would it be possible to extend the intended total operating time? Could maintenance intervals be extended? Is it possible to achieve a more favourable coordination of the inspection times for the entire system and components?
In series tests, we were able to determine whether such optimizations could be carried out without endangering the operational safety of the system. We determine the state of wear, compare target and actual dimensions and make recommendations for the extension of operating and maintenance specifications.
Repair Technology
Damper wheel Stress calculation of an engine block Gear damage
For the repair we develop a repair technology adapted to the special problem. This takes into account the results of a comprehensive damage analysis and contains suggestions for optimisation and new solutions. We develop recommendations for further operation, which make it possible to avoid future malfunctions:
- Provision of new, balanced operating parameters (static, dynamic, mechanical, thermal, etc.),
- Development of solutions for extending the service life of high-quality, expensive components as investment protection,
- New, simulation-based design solutions (incl. manufacturing).
Simulation-Based Root Cause Analysis
Our approach will be explained in more detail using an example.
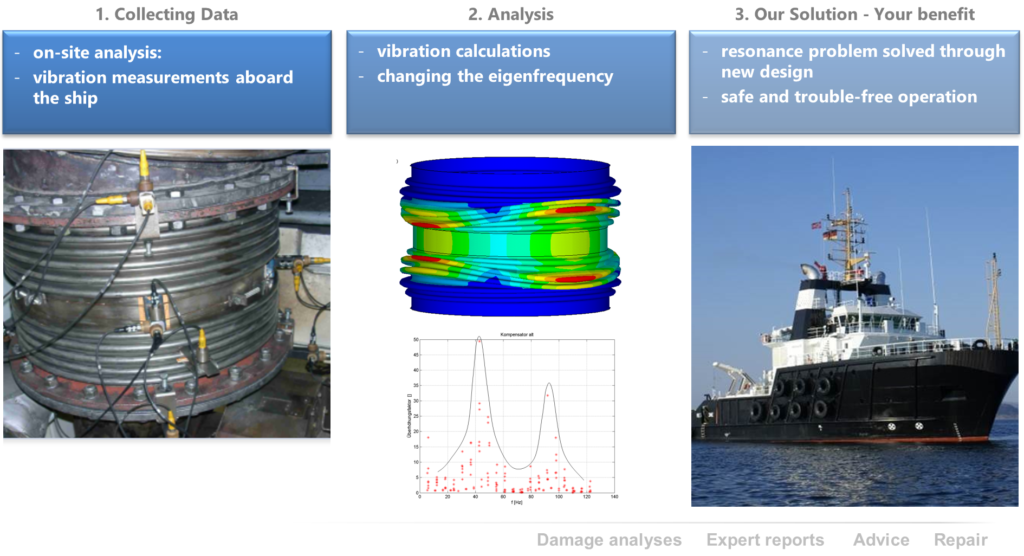
The operational readiness of a deep sea tug was no longer given due to frequent failure of the exhaust system. At very short intervals there were breaks in the compensator of the exhaust system, which led several times to the failure of the vehicle. The inspection in the engine room and vibration measurements on board by our specialists formed the basis for the creation of a numerical simulation model of the conditions on site.
The cause of the damage was determined to be the unfavourable coincidence of the compensator’s natural oscillations with the excitations from the motor. This led to resonances and thus to excessive stress.
With the help of the simulation model, the design of the compensator was optimized so that the tug boat could be used without restriction after assembly of the modified component.